Для обеспечения основательной отделки необходимо удалить все следы и очаги ржавчины. Есть несколько способов удаления коррозии, наиболее распространенным является снятие ржавчины шлифмашинкой. Однако такая обработка сопровождается значительным снижением толщины металла кузова. Более того, происходит нагрев обрабатываемой зоны, приводящий к нарушению внутренних защитных покрытий и ухудшению состояния металла.
Другие способы более эффективны, менее разрушительны, а следовательно, и более предпочтительны.
К сожалению, в автосервисе редко можно встретить пескоструйный аппарат с повторной циркуляцией. Пескоструйная обработка существует давно, но до последнего времени применялась лишь в промышленности, так как для ее организации требуется отдельное специально приспособленное место. Пескоструйные установки без повторной циркуляции бомбардируют зачищаемую деталь гранулами (например, частицами песка), которые под давлением воздуха разлетаются во все стороны со всеми вызываемыми этим процессом отрицательными последствиями. Аппараты с повторной циркуляцией не имеют этого недостатка. Если их применять при меньшей производительности, чем у промышленных аппаратов, то они обеспечат выигрыш за счет облегчения и улучшения условий труда без негативных последствий, а также высококачественное удаление ржавчины. Частицы песка удаляют ржавчину даже со дна пор, не уменьшая при этом толщину детали кузова.
Суть пескоструйной обработки проста: сопло аппарата направляется на обрабатываемый участок, потом нажимается педаль управления, которая открывает выход песку. Песок под давлением сжатого воздуха очищает поверхность и снова засасывается в аппарат.
Уход за аппаратом заключается в очистке и замене фильтров, которые с течением времени выходят из строя.
Для удаления продуктов коррозии (ржавчины) с поверхности металла также пользуются щетками из стальной проволоки (вручную или с помощью механического привода). Такую обработку нужно делать очень осторожно, так как пораженный коррозией металл хрупок и легко повреждается.
Механическую очистку начинают с удаления ржавчины в легкодоступных местах. Труднодоступные места – зазоры, щели, места соединения деталей и установки болтов – очищают от ржавчины стальными иглами и скребками.
Удаление небольшого пятна ржавчины вручную производят грубой (крупнозернистой) шлифовальной шкуркой. Для облегчения работы и уменьшения пылеобразования можно проводить «мокрую» очистку. Для этого поверхность очищаемого металла смачивают уайт-спиритом или керосином и шлифуют.
При проведении этих работ надо учитывать, что очищенная поверхность металла легко ржавеет, поэтому нельзя оставлять очищенные поверхности без защитного покрытия на длительное время.
Рассмотрим порядок шлифования недеформированной поверхности.
Подчеркнем, что во всех случаях операция шлифования кузова требует очень большого внимания, так как качество исходной поверхности должно быть сохранено.
Если выравнивание поверхности производилось с помощью шпатлевок или грунтов, которыми заделывались мелкие вмятины, то шлифование применяют для улучшения состояния поверхности, а не для создания дефектов.
Чтобы обеспечить высокое качество отделки поверхности, необходимо в первую очередь применять большие подкладки. Если отсутствуют промышленные подкладки, их можно изготовить из достаточно ровной деревянной планки. Длина подкладки, применяемой для отделки поверхности, достигает 30 см. В отдельных случаях длина подкладки может быть увеличена сообразно условиям выполняемой работы. Ширина подкладки выбирается равной 12 см. При таких размерах ее удобно удерживать в руках, она обладает хорошей устойчивостью в поперечном направлении и достаточной жесткостью при толщине около 2 см. Подкладку накрывают листом наждачной бумаги, сложенной пополам по ширине, что придает некоторую упругость, не вызывая повреждения поверхности. На первый лист накладывается второй, которым и осуществляется шлифование.
Шлифуют всегда возвратно-поступательными движениями – «вперед-назад». В процессе обработки необходимо обильно смачивать шлифовальную шкурку водой для промывания зоны обработки и самой шкурки. Как можно чаще надо контролировать состояние поверхности обрабатываемого участка визуально или ладонью, совершая движения, аналогичные шлифованию.
Как показывает практика, этот метод обеспечивает хорошее качество поверхности. В то же время мастер с недостаточным опытом проведения работ по шлифованию может испытать значительные трудности при определении поверхностных дефектов. Чтобы повысить чувствительность при контроле качества обрабатываемой поверхности, можно одеть перчатку из тонкой ткани на руку или подложить под ладонь руки тонкую ткань и плавно перемещать ладонь вперед-назад, повторяя движения шлифования.
В процессе обработки шлифовальная шкурка забивается шпатлевкой или краской, поэтому ее также необходимо чаще промывать, чтобы устранить сгустки пыли, которые могут создавать на поверхности глубокие риски. Сильно загрязненную шлифовальную шкурку меняют на новую.
Следует помнить, что полиэфирные шпатлевки шлифуются всухую. В большинстве случаев они пористые, поэтому необходимо придерживаться рекомендаций поставщика. После грунтовки и шпатлевки мастер производит общую шлифовку поверхности, загрунтованной под покраску. Обычно шлифовка производится с водой для устранения пыли и улучшения условий работы. После промывки поверхность необходимо тщательно протереть замшей. Нельзя оставлять капли воды под слоем наносимой краски. В воде содержатся известковые соли, которые выпадают в осадок после испарения воды. Эти мельчайшие частички соли затем оказываются под слоем краски. С другой стороны, грунты очень часто бывают пористыми. Соли удерживают влагу, которая может просачиваться через пленку поверхностного слоя краски и вызывать вспучивание пленки краски, называемое «волдырь». Поэтому перед нанесением лака желательно прогреть обрабатываемую поверхность для удаления влаги. Вместо нагрева можно протереть поверхность спиртом, а затем обдуть из пистолета.
Сплошные ребра на панелях, таких как капот или части крыльев и дверей, зашлифовываются с применением направляющей защитной ленты. Для этого достаточно приклеить клейкую ленту по одну из сторон ребра по всей его длине заподлицо с вершиной ребра. Такой способ позволяет соблюсти прямолинейность ребра в процессе шлифования с деревянной или резиновой подкладкой.
Удаление продуктов коррозии с поверхности металла химическими методами называют травлением. Обычно травление проводят, обрабатывая изделия растворами кислот или кислых солей.
Поверхность предварительно обезжиривают, так как наличие остатков смазки и жиров ухудшает смачиваемость поверхности, в результате чего травление протекает неравномерно. Процесс травления состоит из обезжиривания, травления, промывки водой, промывки нейтрализующим составом, промывки водой и сушки.
Существуют разные химические средства, которые используются для травления. Например, фосфорные кислоты растворяют ржавчину до чистого металла. Кислоту наносят на обрабатываемую поверхность кисточкой. Иногда приходится производить обработку несколько раз, каждый раз зачищая обработанное место металлической щеткой. Протравленные участки промывают чистой водой и сразу же просушивают.
Подчеркнем, что, независимо от применяемого для травления раствора, очищенную поверхность металла после травления необходимо обязательно обработать водой и высушить. Эти операции предотвращают окисление и повторное образование ржавчины. Само собой разумеется, что в процессе обработки деталей кузова кислотой следует защищать открытые участки тела. Во всех других случаях надо строго следовать рекомендациям производителя препарата.
В магазинах есть готовые к употреблению составы для удаления ржавчины с металлических поверхностей. Приведем состав одного из таких препаратов (в % по массе).

Состав наносят на кузов автомобиля кистью, выдерживают 3–5 мин при температуре 20–25 °C, после чего смывают теплой водой из шланга. Остатки кислоты удаляют нейтрализующим составом, который состоит из 47,5 % этилового спирта, 2,5 % нашатырного спирта и 50 % воды.
Часто используются травильные пасты на основе соляной кислоты. В качестве примера приведем состав одной из них:
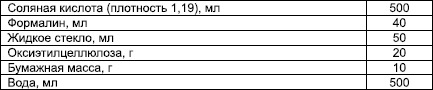
Для получения паст сначала растворяют в воде производные целлюлозы, затем добавляют жидкое стекло и бумажную массу. В образовавшуюся суспензию медленно заливают кислоты и формалин, постоянно перемешивая.
Состав наносят на очищаемую поверхность кистью или деревянным шпателем слоем толщиной 1–3 мм и оставляют на ней на 20–40 мин. Периодически поверхность осматривают, для чего снимают пасту в отдельных местах.
Удаляют травильную пасту с поверхности деталей кузова также шпателем. Для окончательной очистки поверхность промывают водой из шланга, после чего на нее наносят пасту-ингибитор, которая выполняет роль пассиватора.
Пассивирующую пасту наносят и удаляют с поверхности так же, как и травильную. Время выдержки ее на поверхности при нормальной температуре – 30 мин.
После удаления пасты-ингибитора поверхность промывают водой, протирают насухо и сразу же грунтуют.
Паста-ингибитор имеет следующий состав (количество ингридиентов приведено в частях от общей массы).

Пасту-ингибитор готовят следующим образом. Калий хромовокислый растворяют в воде, затем к раствору добавляют сульфит-целлюлозный щелок и инфузорную землю. Паста должна быть однородной, вязкотекучей.
Эффективна смешанная очистка ржавчины. Производят ее так: сначала поверхность очищают механическими средствами, а затем остатки ржавчины в порах металла обрабатывают травильными составами.
Удаление продуктов коррозии – одна из наиболее трудоемких операций при подготовке поверхности под окраску. Облегчить ее может использование преобразователей ржавчины, которые позволяют перевести ржавчину в неактивное состояние. Преобразователи ржавчины делятся на две группы. К первой относят собственно преобразователи, которые только преобразуют продукты коррозии в более стабильные соединения. Ко второй группе относятся грунтовки-преобразователи, т. е. составы, преобразующие ржавчину и одновременно создающие на поверхности металла пленку, которая является грунтовочным подслоем для последующих слоев защитного покрытия.
В качестве примера составов первой группы может служить модификатор П-1Т-Ц, предназначенный для стабилизации ржавчины под лакокрасочными покрытиями. Его используют для преобразования слоя ржавчины толщиной не более 80 мкм.
Этот преобразователь наносят на ржавую поверхность кистью либо с помощью краскораспылителя. При 18–22 °C состав высыхает за 3 ч. Преобразователь в первоначальном состоянии имеет темно-коричневый цвет, после нанесения на поверхность и высыхания он становится темно-синим.
Заметим, что преобразователи ржавчины не взаимодействуют с окалиной, а максимальная толщина слоя ржавчины, как правило, не должна превышать 80–100 мкм. Это значит, что если не снять толстые пласты рыхлой ржавчины, то преобразователи проникнут только в наружные слои пораженной поверхности и процесс коррозии будет беспрепятственно развиваться вглубь под слоем преобразованных продуктов. Важно также строго выдерживать время преобразования, иначе не вступившая в реакцию кислота сама вызовет коррозию.
Указанные недостатки преобразователей в каждом случае надо учитывать.
Торговля предлагает преобразователи ржавчины различных марок. Это продукты взаимодействия фосфорной кислоты с хроматом натрия и окисью цинка. По внешнему виду преобразователи представляют собой прозрачные оранжевые или оранжево-зеленые жидкости. Они негорючи и нетоксичны.
До нанесения преобразователя на поверхность металла ее следует хорошо очистить от грязи и удалить рыхлую ржавчину. Подготовку лучше выполнить металлической щеткой. Затем поверхность надо обезжирить уайт-спиритом, высушить и через 20–30 мин жесткой кистью нанести преобразователь ржавчины, тщательно его растушевывая и втирая в поверхность. Через сутки поверхность слегка увлажняют водой, а через 4–6 суток наносят грунтовку.
Преобразователь ржавчины лигнинный – это смесь, состоящая из аминолигнина, фосфорной кислоты, эмульгатора, коагулятора и воды. Внешне представляет собой маслянистую жидкую пасту темно-коричневого цвета с запахом фруктовой эссенции. Этот преобразователь также негорюч и нетоксичен. Преобразует слой ржавчины толщиной до 150 мкм, легко удерживается на вертикальных и потолочных поверхностях. Лигнинный преобразователь ржавчины можно применять как при положительных, так и при отрицательных температурах. При комнатной температуре процесс преобразования ржавчины длится 16–20 ч, при 100–110 °C – 15–20 мин.
Допускается нанесение этого преобразователя на влажную поверхность, однако перед нанесением поверхность нужно очистить от грязи, рыхлой ржавчины и обезжирить. Преобразователь можно наносить кистью, валиком и краскораспылителем. После обработки поверхность кузова приобретает цвет от серого до темно-коричневого (цвет зависит от марки стали и характера ржавчины), не имеет вздутий и не шелушится. Обработанную поверхность оставляют на 16–20 ч, после чего грунтуют. Этот преобразователь превращает ржавчину в водонерастворимые химически стойкие соединения, прочно связанные с поверхностью металла.
Надо учитывать, что стойкость покрытий, нанесенных на поверхность, обработанную тем или другим преобразователем ржавчины, как правило, ниже, чем стойкость покрытий, нанесенных на очищенный от ржавчины без преобразователя металл.
Еще одно замечание: при нанесении преобразователей ржавчины необходимо следить, чтобы они не попадали на поверхности с не удаленным лакокрасочным покрытием, так как содержащаяся в них фосфорная кислота и комплексообразователи, не вступившие в реакцию с окислами металла, снижают адгезию наносимых покрытий.